Interview: In the frame with Jo Williams
WCL visited Jo to find out how and why she rescued eight tonnes of native timber, otherwise destined for landfill and how her framing and supply business is developing.
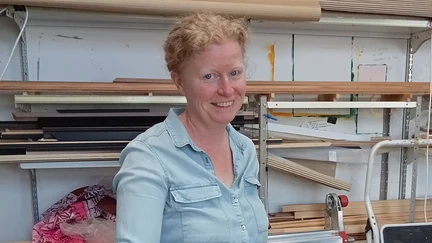
Eight tonnes of recycled wood takes up a bit of room, but surprisingly not as much space as one might expect. Jo Williams of J.W. Framing & Supply in Newtown, used a Wellington City Council Organics Diversion Fund grant to rescue the native timber when the Wellington Girls’ College auditorium was demolished. Now Jo’s in the process of breathing new life into it.
WCL visited Jo to find out how and why she rescued eight tonnes of native timber, otherwise destined for landfill and how her framing and supply business is developing.
" I’ve got three businesses going on within this space."
WCL: Tell us a bit about what led you to setting up a picture framing business?
JW: I moved here from Hamilton. I had a museum background and I couldn’t find work in my field. I didn’t want to abandon that career so I decided to go out on my own.
WCL: How did you learn the necessary skills of framing?
JW: From working in the Waikato museum (Te Whare Taonga o Waikato) framing art works for exhibition. I got so much out of that experience. I remember framing a Seraphine Pick watercolour and thinking “This is so cool”. It provided me with opportunities not many people get.
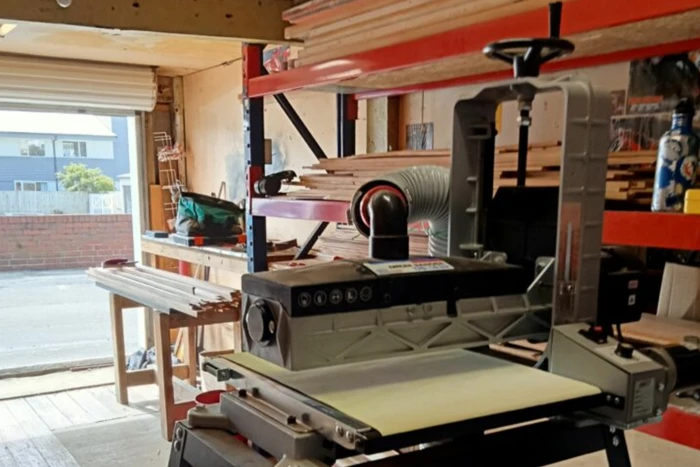
WCL: When you went about setting up your business, how did you do it? You’ve got a lot of stuff in your studio.
JW: I’m in my fourth year of being full-time. I was two years part-time at first. I knew someone who’s father-in -law bought a retiring framer’s equipment and was going to start his own business but never did. So I bought that stuff off him for five grand. I got three basic pieces of equipment to set up and a little bit of stock as well. The equipment wasn’t the greatest but it got me started.
I started in my bedroom in a flat up the road where I was living in at the time. I then got a sliver of workshop upstairs [in the present complex]. I used the workshop for cutting frames and ferried them back to my bedroom for completion.
I worked part time while just practising for six months.
My first job was for Thumbs Up, a group of disabled artists in Petone.
Friends and neighbours supported me and it just sort of grew from there. I moved into a bigger workshop space, then I moved into this present studio space.
I got a sign and stuck it out on the street “Open Saturdays” and work started coming in. It enabled me to go full time four years ago.
Business came very much from the Newtown community. I have customers around the neighbourhood.
And then the website was developed. People just google “Picture framing Wellington”. It’s nice to have an easily describable business. It’s easy to google.
I find the best thing for me is to be open Saturday. I’m open 10 to 3. Anyone can walk in at that time. If they don’t, it doesn’t matter. I just do my admin during that time. It sucks working weekends sometimes but that structure is the steadiest thing I have in my working week.
My working week can be all over the place so having that regular Saturday time for doing that is really good.
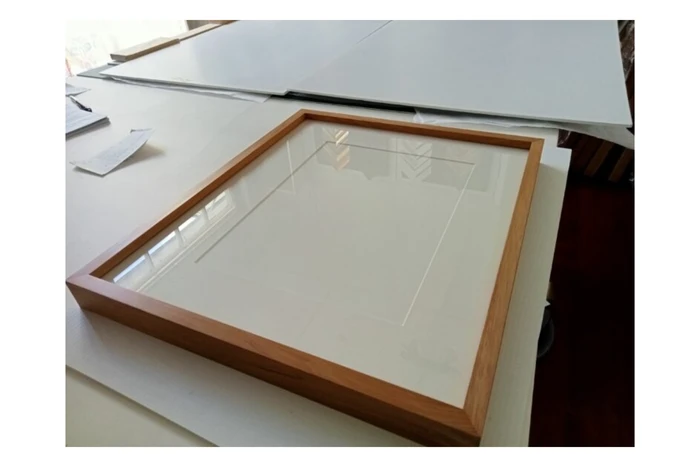
WCL: Have you had to learn to cut glass as well and get equipment for doing that?
JW: You don’t actually need very much equipment for glass cutting. You just need practice and a steady hand. It’s all about measuring. Measuring and accuracy – you have got to have everything accurate to like, point five of a millimetre with glass.
This stuff is all about measuring. And I’ve been through hell.
When I was at the museum I got thrown in the deep end and had to practice and practice and practice. I had a couple of people I could ring and one was the framer at Te Papa and I still ring him up now and go “Help!” He’s become a mentor.
That struggle though, at that time, is probably what gave me the grit I needed to do this.
WCL: What else do you do besides framing?
JW: I hang art in people’s houses. That’s been a great addition to the business.
WCL: Talk us through how an art hanging service works
JW: First of all, if there’s a really heavy or large item that needs a professional to hang it. It needs proper fittings so it doesn’t fall off the wall. Heavy mirrors or really big paintings. Then there’s the aesthetic side – you try to make it work in the whole room so there is a flow.
I try to make it feel calm. And also – you hang things on two hooks so they don’t go crooked.
WCL: Besides art works what other things have you been asked to frame?
JW: A couple of people want me to make a magnetic frame or something for their kids art and family photos so they can swap them out. I’ve framed a few kids’ art and when they see their art trapped in behind glass and in a frame, they don’t generally like it.
So I have a vision and need to design something where you can just swap them out and easily access them and kids can do it themselves.
I have a customer whose father built a log cabin, not having done anything like that before. They want me to make something unconventional with a rustic feel. So that’s a fun challenge. I do like the bespoke challenges.
In the early stages those things were actually quite … you’d end up working for hours and hours and get paid next to nothing. So you get better at saying no to things. But it’s also how you develop your skills. There’s a fine line between getting the experience and getting paid.
WCL: How did you work out how to charge out your services? Did you look at what other people were charging or have you come up with a figure that works for you?
JW: I come from a community arts background and I struggled a lot with charging enough. I think I’m there now where I’m happy with the rate I charge.
I have a rough idea of what other people charge. It’s just sort of testing the waters and getting confidence up.
You punish yourself and think “I should have done that faster.” It should have taken two hours but actually I did it in four. But then your confidence grows and you think “No, it takes three. Do it in three, charge for three”.
The thing about self employment is that you don’t get to measure yourself against anyone else. When you’re working alone you don’t really see how other people work. In the past year or so I have worked alongside other art hangers and have learned from them.
It’s what the customers say. If they’re happy, then that’s good.
WCL: Do you prefer working with wood?
JW: Yeah. The workshop upstairs is my happy place. This whole thing is about precision but the workshop and wood is a little more forgiving. Working with the recycled timber is great compared to working with the painted surfaces of commercial mouldings. I definitely like working with the wood most of all out of all the processes.
WCL: Is it mainly recycled native timbers?
"Yes. There’s just so much around and it’s getting wasted. It’s such beautiful stuff and so much better than anything you can buy new. If you take the time to turn it back into something beautiful.
It brings a warmth into the room."
WCL: You applied for, and were awarded, a Wellington City Council Organic Waste Diversion Fund. Tell us a bit about the process of applying for the grant and what have you done with the funding.
JW: I think the funding applications opened around Christmas time. I didn’t actually know about it and somebody brought it to my attention. Lots of people were encouraging me to apply for it. I had received $2000 funding the previous year from the Waste Minimisation Fund to buy a thicknesser to do the same thing I’m doing now but on a smaller scale. It was a small step forward.
I thought “No way. I won’t get that. I’m not ready for that” but the universe was saying “Do it! I have experience at applying for funding with some of my past jobs so I thought I’d give it a go. The people in the Waste Min team were really supportive and I could go to them with questions and they were really helpful. It’s a newish fund, only about three years old.
I come from an arts background where there is so much competition for funding, so I was used to doing quite tight applications. I was amazingly lucky enough to be successful.
What have I done with the money? Well, I bought equipment, machinery and I’m paying someone to help me get this whole thing going. Dustin is a qualified joiner and is helping get the whole recycled timber enterprise off the ground.
I got the guillotine. I used to cut everything with a craft knife for three years, which was ruining my arms and doing my head in. If your ruler is out by point five of a millimetre then you end up with a rhombus. Just cutting a perfectly square rectangular piece of cardboard can be a world in itself without decent tools. So the guillotine has been an absolute game changer. It speeds me up a lot, helping to make the process more production oriented. Instead of every single thing having to be done from start to finish and then you start the next one. It’s just too slow. I can now work in a much more efficient way.
There’s a machine upstairs, a woodworking machine that can do a whole lot of things, and there’s other machinery, like the metal detector.
WCL: Is all this machinery available in New Zealand or have you had to import some?
JW: It’s all New Zealand. Some is second hand and some is new.
WCL: As a recipient of the grant what expectations are there on you, from the council, to account for how the funding is used?
JW: I submitted a budget with my application and I have to report back with my actual spend. My main objective was to save eight tonne of wood and that’s what they really liked. I’ve met that objective.
WCL: Is this wood that would otherwise be destined for the landfill from demolished buildings? How do you find out that wood is going to become available?
JW: All of the eight tonnes comes from Wellington Girls’ College auditorium. There will be other buildings in the future.
I have a relationship with a demolition company. There’s a guy, Matt Thornton, of Ceres Environmental NZ, who came here. We just happened to start talking about wood and I showed him the samples that I was using. He said “Oh, I can get you a lot of wood” because he’s got an interest in sustainability as well. Having worked in the demolition industry he’s seen masses of demolition timber be taken to the tip everyday.
His boss, Swaroop Gowda, kindly wrote me a letter of support for the application which formalised our arrangement. I was so stoked.
At the moment I’m still trying to figure out how to deal with it all in an efficient, productive way. I’ve learnt so much. When this is processed and sold then more will come in from other places.
WCL: Who is your market for eight tonnes of recycled native timber?
JW: I want to see other framers using my timber. I’m going to wholesale the prepared timber to framers around the country. That’s what I’m working on. It’s a premium product. There’s been massive learning curves because I’ve never machined any timber in my life before now.
WCL: Do most people want to leave the wood in its natural state or do they want it painted?
JW: Most people love it as it is. Rimu goes with pretty much everything. Some people have had bad aesthetic experiences with rimu in the 90s, such as yellow varnish. I have to be very careful with my design. I also have a lot of what might be red beech (tawhai raunui) which will probably be stained as the colouring varies a lot.
I still have all those samples of commercially available mouldings there, but 80 percent of the time this is what people are choosing. I’m looking at having six to eight of my own mouldings by the end of the year. I’m not going to be too complicated. The simple stuff is quite fashionable at the moment. People want simple, box framing. They don’t often want fancy stuff with curves and ornate gold stuff. Having it there shows people what they don’t want.
WCL: Have you marketed the recycled framing specifically to WGC alumni as a nostalgia thing?
JW: I haven’t really done any marketing yet. Alys Freeman (Business Development Manager, WGC) put something in the newsletter to the alumni before Christmas and the Council did an article to promote the fund being opened again, so I got a lot of people contacting me when that came out. I now have a mailing list for people who want frames made with the wood from the Auditorium.
I’ll soon have some premade frames available for purchase. There’s a lot of nostalgia attached to it. Custom framing is prohibitive for most people so I’m trying to make some keepsake that’s affordable.
WCL: You talked earlier about being on your own and not being able to compare yourself to what others are doing. What other upsides and downside are there to running a small business?
JW: It does feel really isolating sometimes. For the first three years I was here I was living here, working here. I was broke and it was a struggle. I thought about quitting so many times and looked for other jobs. But I kept going. I think the customers probably kept me going. I meet really interesting people that I wouldn’t normally meet and I think I make friends with all of my customers.
This timber thing has got me through I think. Everything has been saying “Do it, do it, do it” the whole time. The path is already written and I just have to walk it.
WCL: Like the serendipitous meeting with Matt?
JW: Yeah. I said to someone the other day, this whole thing has been like stumbling down a corridor in the dark, not knowing what obstacles are there. But I just keep going and it seems to be ok.
WCL: Do you have any advice you’d like to share with anyone thinking of starting a small business of any kind?
JW: Just persevere. Keep going. Keep your standards high. Just keep going as long as you can. It is really good being self employed.
WCL: Future plans?
JW: I’m really interested in innovation and sustainability and would love to dive deeper into this field. It would be amazing to be able to develop other products that can help clean up the world.
I’m hoping in future to do framing lessons. Artists are struggling and framing is a hideous barrier for them. I would like to be able to facilitate them being able to do it for themselves.
"My passion is helping artists.
I like variety, I like a challenge. I like my neighbourhood and community.
Plus I have an awesome Metal Detector if any DIY woodworkers want to come and use it!"
Click here for more information on the WCC Waste Minimisation funding.